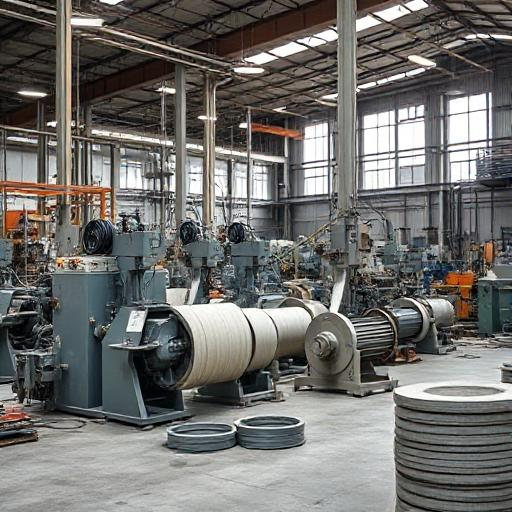
Cogged V-Belt Manufacturing
Share
In this post we will explain briefly how cogged v-belts are produced. Cogged v-belts are typically more high-performing than their wrapped counterparts. This is due to increased flexibility, grip, and heat resistance.
1. Compound is Mixed
Most producers mix their own proprietary compound in-house based on customer requirements and R&D. Nearly all high-quality v-belts are now produced from EPDM (ethylene propylene diene monomer). This is heat resistant compound commonly used in roofing. Reinforcing fibers, carbon black, and other ingredients are added to get the rubber properties just right.
2. Compound is Calendered
This step takes the rubber and squeezes it between large roller to form a consistent sheet. The sheet is trimmed and stored on rolls.
3. Belt is Assembled
Next, the rubber and tensile members are wrapped around a steel mold. Picture a steel barrel, with the diameter depending on the size of the belt being produced. Tensile members are typically made of highly engineered polyester fibers, twisted together and chemically bonded. A flexible mold is placed over the steel mold / rubber. This mold has cogs in it and acts like a blood pressure cuff, squeezing into the rubber.
4. Belt is Cured
Now the whole assembly is placed into an autoclave, or steam pressure vessel. The steam pressure pushes the cog shape into the belt and cures the compound. Curing causes molecules in the rubber to bond together, making it one homogeneous piece.
5. Belt is Cut
The belt is then cut into individual pieces using several pieces of sophisticated equipment.
6. Belt is Inspected and Packaged
Workers inspect belts for any defects and for proper labeling, count, and package the belt per customer requirements.
Now the cogged v-belt is on its way to power our world!